RESEARCH
Our Motivation
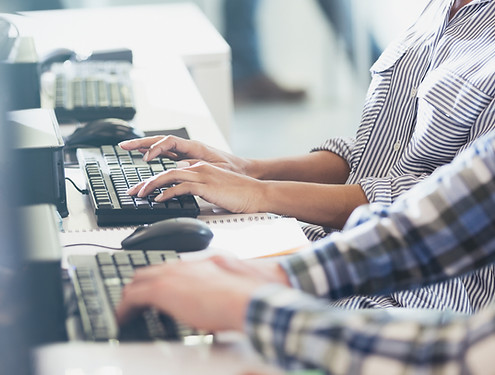
Our research vision is to bridge strengths between additive manufacturing, computational mechanics, and material design by properly characterizing the uncertainties of different manufacturing processes and incorporating them in designing and optimizing architected materials. I am particularly interested in developing reduced order and surrogate models, exploiting machine learning techniques to speed up computational optimization. On the other hand, we seek to overcome the maximum printing size restriction imposed by additive manufacturing by avoiding manufacturing large macro-structures as a single mechanical part. Instead, the concept of assembled architected materials employing discrete building blocks jointed by mechanical sutures is used.
Our research work has been shaped by my deep interest in the field of dynamics and in how uncertainties inherent to manufacturing processes affect the prediction, design, and performance of mechanical systems. Recently, we have become particularly interested in architected materials, a class of engineered structures exhibiting properties typically not found in nature, able to perform multi-functions previously considered mutually exclusive. My major motivation is to explore using architected materials in new applications related to clean energies, health, and human safety.

Design and Optimization of Architected Material Subjected to Manufacturing Uncertainties
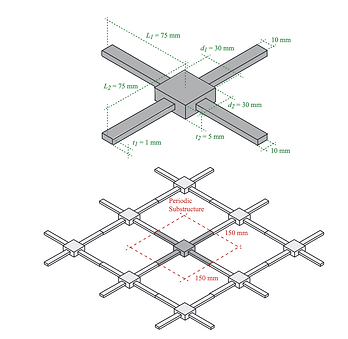
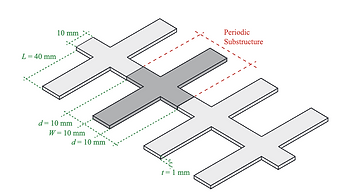
The proposed research contributes to intellectual merit by advancing the design and optimization of architected materials, explicitly addressing the challenges associated with large-scale substructural arrays and manufacturing uncertainties. The proposed computational procedure integrates a Component Mode Synthesis method with Machine Learning surrogate models previously trained using a database of precomputed substructures. The framework enables the efficient system-level modeling of architected materials without the need for remeshing or recomputing mass and stiffness matrices. This approach not only addresses the computational challenge of assembling a large number of substructures but also facilitates the development of reduced-order models. Additionally, the proposed framework incorporates stochastic simulation techniques for uncertainty propagation, allowing accurate prediction of physical responses considering manufacturing uncertainties. The research significantly contributes to the field by providing computational tools for analyzing complex metamaterial configurations and gaining insights into their behavior under uncertain mechanical properties and geometrical characteristics.
Adaptable and Resilient Architected Materials Assembly with Bi-stable Discrete Building Blocks
Mechanical bi-stable structures utilize mechanical instabilities like snap-through to perform structural transitions to other stable states. The inclusion of bi-stable building blocks in architected materials opens new and exciting possibilities; depending on the design of the bi-stable building block, these new materials may possess a combination of unique properties/behavior, such as the ability to undergo large reversible deformations, "shape memory" effect, reversible pseudo-plasticity, and controlled hysteresis. A promising feature of these materials is that one can control their macro-scale behavior by properly designing the bi-stable building blocks.
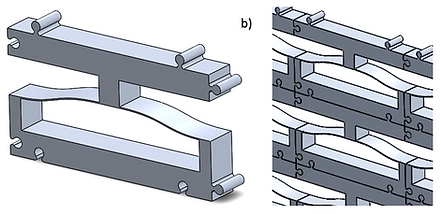
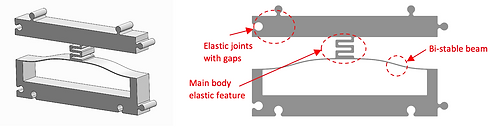
A particular case of interest is using bi-stable lattices to enhance energy absorption or shock isolation. However, one of the challenges is the difficulty of manufacturing large macro-structures as a single mechanical part. To overcome this issue, this proposal is based on the use of discrete assembled building blocks. These blocks can be designed and fabricated separately, and the compatibility at their boundaries guides their assembly.
Complex structures and geometries can be constructed by precisely defining the positions and orientations of these blocks. This strategy offers several advantages: (1) the discrete nature of the blocks and their assembly allows for the detection and correction of assembly errors, (2) different types of blocks or materials can be combined in the assembly process, expanding the range of possible designs and functionalities, and (3) it facilitates disassembly and reuse.


Early models of architected materials predominantly incorporated regular unit cell structures. However, with the rise of additive manufacturing, producing highly complex structures on various scales and materials has become feasible. Despite this advance, employing additive manufacturing for structures derived from numerical designs presents two substantial challenges: (1) constructing large metastructures within the limited printing size constraints of additive manufacturing machines and (2) ensuring reliability in predictions accounting for manufacturing uncertainties. In this sense, the scalability of architected materials can be achieved by stacking and fixing discrete building blocks. In this project, the concept of mechanical suture will be explored as a joint mechanism between adjacent building blocks.
Mechanical Sutures as a Joint Mechanism for Architected Materials
This mechanical suture is inspired by structural biological materials, where Jigsaw-like joints provide a bonding mechanism between dissimilar materials. The principle of operation for these joints is based on geometrical interlocking between two structures. The interlocking geometry is usually defined based on semi-circles or elliptical shapes due to their capabilities to handle stress concentrations and large displacements. However, the current models overlook the effect of horizontal and vertical gaps between the connected structures - a feature that potentially facilitates the assembly of a large number of building blocks, especially when the manufacturing process lacks precision. The goal of this project lies in the influence identification of these joints on the macro-structure performance of architected materials, which remains unexplored in the face of harmonic, cyclic, and impact loads. Questions concerning the optimal number of joints, their best geometry, and permissible tolerances are due for investigation.